
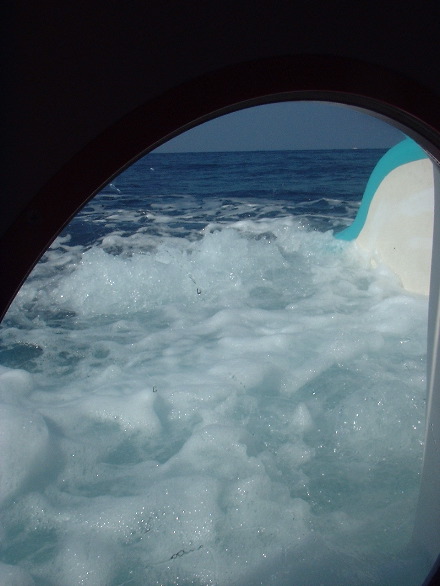
The CAD model is more detailed than is needed for the simulation, so automatic de-featuring increases simulation performance. The model geometry was built with CATIA roles, with parameters allowing optimization later, and therefore it can be made immediately available for simulation on the 3DEXPERIENCE platform.
Bow wave underwater submarine surface full#
The project begins by making full use of the “Requirements, Functions, Logical and Physical” (RFLP) data model to build the CAD model shown in Figure 1. As soon as the initial CAD model of the hull is available, work can begin. The sooner stealth factors are considered, the less risk there is of problems being found late in testing, and the more potential there is to find an optimal solution. The workflow to reduce detectability begins early in development. Stealth Design Workflow Modeling the submarine Figure 1: View of the external casing of the entire military submarine model This means naval architects, radar engineers and computation fluid dynamics (CFD) experts all need to work together in a multi-domain, multi-objective workflow. To maximize stealth, we need to be able to deal with both these effects at the same time.
Bow wave underwater submarine surface free#
For undersea vessels near the surface, this is further complicated by hydrodynamics as the wake produces a complex free surface deformation pattern. Therefore, one of the basic principles of stealth design is to minimize the back-scatter. The waves that are back-scattered towards the receiver are what allows an enemy to detect the submarine. When radar waves strike the vessel, they are reflected and scattered. A poorly optimized design produces excess noise and increases the vessel’s detectability.Īnother important factor is the radar cross section (RCS). The sound is not just a result of vibrations and noise from machinery inside the vessel – the hydrodynamical design of the hull itself affects noise as water flows turbulently, particularly around control surfaces. The noise signature of a submarine affects how readily the vessel is detected by passive sonar. The detectability of a submarine depends on several factors. This blog post will demonstrate how MODSIM, unified modeling and simulation, enables the development of modern undersea defense technology, using stealth design as an example of the benefits of a MODSIM approach. This means submarine development requires large teams with many different specialist groups working together to produce a fully capable vessel that can carry out undersea defense objectives. Its hydraulic, electrical, thermal, ventilation and mechanical systems are safety-critical and all need to operate reliably for months on end. It must travel with minimal drag as silently as possible while also minimizing its radar cross section. A successful, safe and reliable underwater vessel design must be able to withstand the pressures of deep ocean water and the stresses of waves – and the shock impacts of combat. Submarine engineering is a challenge – there are few areas of engineering that require such precise control of as many different domains of physics. A unified approach to modeling and simulation (MODSIM) allows the simulation results to inform the design, shortening the development process to produce a submarine that achieves stealth requirements without compromising other objectives. Simulation can be used to analyze the RCS of a semi-submerged submarine in motion, and to optimize the geometry to minimize the RCS of the wake. The radar cross-section (RCS) of a submarine at the surface depends not just on the geometry of the vessel, but also the hydrodynamic wake on the water surface. Stealth and detectability are a critical aspects of the design of a submarine.
